What is supply chain management?
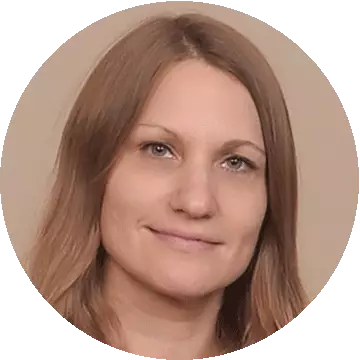
Written by Camilla Andersson
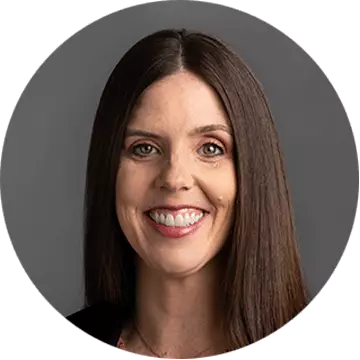
Reviewed by Kathryn Uhles, MIS, MSP, Dean, College of Business and IT
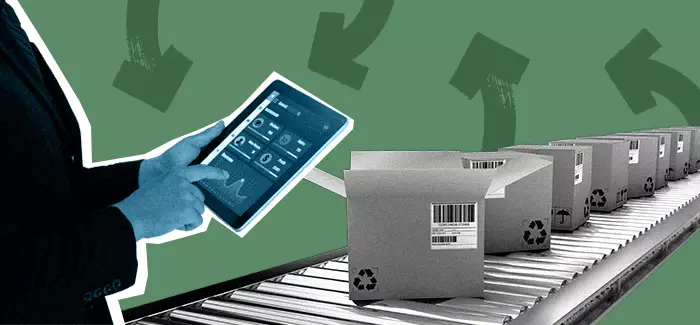
Have you ever wondered how products get from production to your cart? It’s a multistep process that involves several parts of a business and is referred to as supply chain management. Let’s take a look at how supply chains operate, where they are used and recent developments in the process.
What does a supply chain management department do?
Supply chain management (SCM) departments ensure everything progresses smoothly as products move from manufacturing to sales. These departments focus on production, logistics and distribution, addressing such concerns as the delivery of materials to the factory, quality control and timely distribution.
Supply chains can be divided into two parts: upstream and downstream. Upstream refers to the steps involved before the manufacturing stage, such as purchasing, shipping and storing raw materials. Downstream refers to the processes involved in getting the products from the manufacturer to the customer.
Companies that manufacture their own products use suppliers to provide components or parts. Other companies outsource manufacturing to contract manufacturers (CMs). Still other companies don’t manufacture or outsource manufacturing but simply sell finished products supplied to them. Each of these business categories has a supply chain that may include one or both upstream and downstream responsibilities.
These are some of the main components of the supply chain:
- Planning: Each step of a product’s journey through the supply chain must be identified and plotted out, from determining how a factory’s location impacts delivery to how the product will be distributed to customers.
- Sourcing: Sourcing refers to vetting, choosing and overseeing suppliers.
- Manufacturing: This step involves overseeing production, including the flow of goods to and from factories.
- Distribution: This refers to the processes that get the final products to end users.
- Returns: In supply chain management, this step involves the logistics of processing products consumers decide not to keep (e.g., how to ship and restock them) as well as tracking the reasons why consumers are making returns.
A small company that sells a simple product may not have a dedicated department to manage its supply chain, but it very likely has the same steps embedded into its structure. So, where a large company might have different departments for different steps in the supply chain, a small company might have various departments integrate supply chain steps into their roles. Companies can also outsource supply chain management.
Many job titles are related to supply chain management , but one you may have heard of is supply chain manager. Working in this field requires organizational and analytical skills and attention to detail. Basic IT knowledge is also helpful because modern supply chain structures rely heavily on IT. A general understanding of business and economic concepts can also be beneficial. Managers typically hold at least a high school diploma.
Supply chain risk management
Supply chain management is essential for several reasons. Supply chain issues can affect the quality of the final product. If a supplier provides subpar parts or components, the final product might be less durable or not work as intended. This can lead to negative reviews, high product returns or lawsuits.
In some industries, such as electronics, medical devices and vehicles, product failure can result in injuries or worse. Therefore, such industries must follow stringent regulations for manufacturing and quality control.
Other issues that may occur in the supply chain include problems during storage or shipping, which can cause delays in getting the product to market. This can lead to the company losing money or not meeting its financial goals. A disorganized supply chain can also impact consumer views of a business in other ways. For example, a consumer may decide to shop elsewhere if the return process is too complicated.
Even when the supply chain works as intended, strategies to optimize it can reduce costs, improve customer satisfaction and increase revenue. However, not all supply chain factors are under the company’s control. Unexpected changes can disrupt the production, shipping and distribution of goods. These are called supply chain disruptions. Factors such as weather, accidents, local conflicts, strikes and natural disasters can cause sudden supply chain disruptions. While these changes can happen unexpectedly, companies can prepare by creating plans for potential disruptions. Other supply chain disruptions, such as labor shortages, pricing fluctuations, changes in consumer demands and regulatory changes, can develop more slowly.
Planning for supply chain disruptions is part of a supply chain risk management strategy. An effective risk management strategy focuses on identifying, preventing, preparing for and responding to vulnerabilities in the supply chain.
These are some strategies to increase supply chain efficiency and reduce risks:
- Select suppliers that are reliable and communicate well
- Have more than one supplier in case a shortage or quality problem occurs with an existing supplier
- Create and maintain good relationships with suppliers
- Inspect suppliers or hire third parties to do so
- Stay up to date with and incorporate new technologies
- Stay up to date with regulatory developments and other factors that can impact the market
- Conduct risk assessments and create plans for supply chain disruptions
Phases of supply chain management
The first phase in supply chain management is planning and forecasting. During this phase, a company estimates customer demand and plans what volume of raw materials, components or products to order.
The second phase is sourcing and procurement. First, a company seeks vendors and signs contracts. Then, the company communicates with vendors and receives products. It might also inspect manufacturing facilities and renegotiate prices and contracts. Sometimes, a vendor must be replaced if it doesn’t meet performance or quality goals.
The third phase is inventory management and logistics. This phase includes tracking, storing, shipping and distributing goods.
Types of supply chain models
Lean supply chains focus on efficiency, cost savings and waste reduction. Agile supply chains are designed for flexibility and adaptability.
Lean supply chains are used by companies that don’t expect many disruptions or significant changes in market conditions. This enables them to cut costs and reduce waste, but the resulting smaller inventories and fewer staff can make a company more vulnerable to supply chain disruptions should they occur. Lean supply chains are common in the automobile industry since minimizing inventory reduces costs like storage space or unsold vehicles.
Agile supply chains are typically used by companies that anticipate a large number of disruptions, such as fluctuating product demand (as in fast fashion) or production locations where local conflicts or strikes are common.
A lean supply chain can be part of a sustainability strategy. A sustainable supply chain focuses on reducing the environmental impact of production, shipping, transportation and other aspects of the supply chain. Companies might create a sustainable supply chain to meet regulatory requirements, ethical responsibilities, customer demand, cost reduction goals or a combination of these factors.
Sustainability can be part of a corporate social responsibility (CSR) strategy to make a positive impact and build brand awareness. Some companies use the term ethical supply chain or responsible supply chain to target not only sustainability goals but also the social impact of a supply chain, such as the working conditions at factories.
In the end, companies don’t necessarily need to choose between lean and agile supply chain approaches. In some cases, a balance between the two may be ideal.
Developments in supply chain technology
As technology advances, some companies may find it’s easier to not only react to disruptions but to predict and prepare for them. This change is part of the transition from traditional to modern supply chain models.
Traditional supply chains focus on manual processes, such as data entry. They have limited options for communication between suppliers, manufacturers and distributors. Due to limited real-time data, it’s also difficult to track goods through the supply chain, which is referred to as visibility.
In contrast, there are now companies that use integrated supply chains, which means that stakeholders, such as manufacturers, suppliers and shippers, are connected through IT solutions. This can minimize silos and improve standardization.
Modern supply chain models also include a range of data, analytical information and technologies. These tools help companies automate processes, make predictions, increase efficiency, prevent risks and respond quickly to changes. Think about robotic process automation, for example, which automates manual tasks. Or the Internet of Things (IoT), which are devices that can provide real-time data and predict equipment failures.
Another example is AI, which can be used to analyze data, assess risks and make forecasts.
Emerging technologies continue to transform the industry. For example, blockchain technology improves the ability to trace devices, which can prevent counterfeit products. This is especially important in the healthcare industry.
The technological advantages of modern supply chains have also resulted in a cultural shift, where stakeholders communicate and collaborate more than in the past. For example, providing real-time status updates and order tracking. When suppliers, manufacturers and distributors work together, everyone can benefit. For these and other reasons, supply chain managers are wise to stay abreast of new technologies and developments.
Want to learn more about supply chain management?
Supply chain management is part of operations management, which involves various phases of business planning. University of Phoenix offers a certificate in this field. The Operations Management Certificate includes courses in purchasing and procurement, logistics management, strategic supply chain design and more.
If you’re interested in a bachelor’s degree program, you may want to consider a Bachelor of Science in Business with an Operations Management Certificate .
To learn more about the university and how to enroll, get in touch with an enrollment representative .
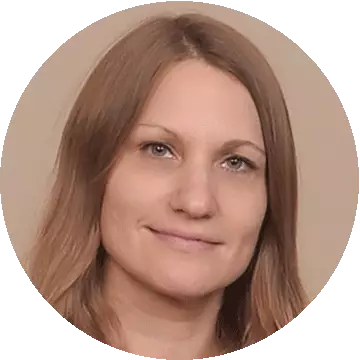
ABOUT THE AUTHOR
Camilla Andersson is a writer with a degree in journalism. She has written and edited content for trade magazines, blogs, white papers and newsletters. Camilla lives in Los Angeles and is a graduate of San Francisco State University. She grew up in Sweden, where she published her first work, an op-ed in the newspaper Aftonbladet, at the age of 15.
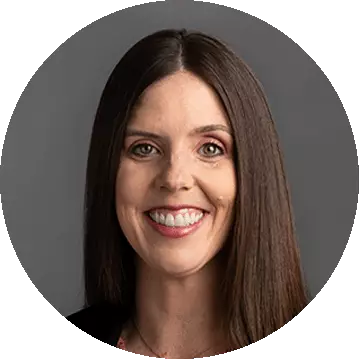
ABOUT THE REVIEWER
Currently Dean of the College of Business and Information Technology, Kathryn Uhles has served University of Phoenix in a variety of roles since 2006. Prior to joining University of Phoenix, Kathryn taught fifth grade to underprivileged youth in Phoenix.
This article has been vetted by University of Phoenix's editorial advisory committee.
Read more about our editorial process.